Flexible, Resilient, and Multiscale 3D printing
​
We have developed material extrusion based additive manufacturing capabilities for breaking the endemic resolution-throughput tradeoff that plagues such processes, enhancing material properties to near bulk values, enabling unprecedented resilience to printhead failure, and enabling previously unseen flexibility in printing large or small objects with high geometric accuracy and minimal material/energy waste. More to come very soon.
Damage-free Large-area nanoparticle fusion for printed planar electronics
​
Solution printing nanomaterials into patterns and films is a highly scalable approach for printed electronics with applications in energy, healthcare, separation, & sensing. We work on an equally scalable process for the critical subsequent step of nanomaterial fusion, i.e., Flash-Light-Sintering (FLS) or Intense Pulsed Light sintering (IPL), to solve the issue of rapid but low-temperature fusion. FLS is inherently capable of feet/ms throughputs. We have shown:
-
Record high electrical conductivity for metallic nanoparticles at feet/ms throughputs and low temperatures of 125C.
-
​
-
Alleviation of conductivity-flexibility tradeoffs and blowoff defects via mixing nanoparticles of different shapes.
-
Control of crystalline phase, electrical properties, catalytic behavior and optical properties in semiconductor nanoparticles.
-
Scalable in-situ chemothermal synthesis of complex multielement alloys from easier-to-fabricate simple alloy nanoparticles.
​
-
Nanomorphology-dependent bidirectional coupling between fusion and heating in FLS, which can be used to control porosity depending on the required functionality.
-
Mutliscale physics-based modeling of process-structure-property relationships in nanowire fusion.
-
Nanowires experience unexpectedly large dynamic self-alignment during fusion, enabling much greater conductivity than expected.
-
Fusion between dissilimar-shaped nanoparticles does not follow conventional paradigms, but is regulated by dislocation generation due to surface recrystallization.
​
This project is funded by the National Science Foundation.

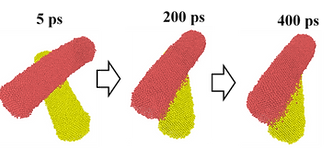
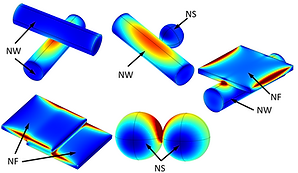
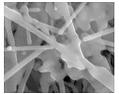
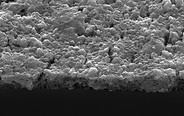



Damage-free 3D printing of structural electronics
​
3D electronics embedded inside 3D solids can enable the next generation of multifunctionality and structural miniaturization in transporation, energy, sensing, robotics, and healthcare applications. The combination of 3D printing of the structure and nanoparticle printing for the electronic circuits is naturally suited to the above fabrication. However, this approach is currently limited by low circuit conductivity or thermally limited material window of the structure.
We have combined nanoparticle printing and FLS with 3D printing of polymers to break this tradeoff and achieve a high conductivity of 11 microohm-cm even with a very sensitive polymer material like PLA. We have further discovered an unusual effect of 3D printing on the conductivity of the printed circuits and that the 3D printing parameters influence this phenomenon.
This project is funded by the National Science Foundation in collaboration with Dr. Howon Lee at Rutgers University.




Form-Fuse process for material-agnostic & scalable conformal electronics
​
Electronics that conform to a 3D surface have significant emerging applications. We have combined the large-area capability and high throughput of nanoparticle printing, flash light sintering and vacuum forming, to create a hybrid process which can make conformal modular electronics that are robustly attachable to a targeted 3D surface. This process completely eliminates thermal damage in direct conformal printing thus significantly expanding the object's material window, reduces the material cost and chemical usage in electrochemical deposition methods, & increases the size of the 3D surface size. Further, the modular nature of the electronics enables easy replacement.
This project is funded by the National Science Foundation in collaboration with Dr. Chih-hung Chang at Oregon State University
​
​
We are directly combining electronics and fabrics via sustainable, cost-effective and scalable manufacturing processes. To achieve these goals we have combined printing and synthesis of electronic and semiconductive nanomaterials with flash light sintering. Our recent successes include fabrication of (1) highly conductive and conformal nanowire films and patterns on thermally sensitive low-cost woven polyester fabrics for personal heating and plasma decontamination (2) negative temperature coefficient thermistors on low-cost woven polyester fabrics with parity in performance with commercial non-fabric thermistors.
​
We are working on using fungi-derived biopigments within inkjet printing and thermal processing to create a sustainable paradigm for fabric dyeing. Such fungal biopigments do not need toxic chemicals to produce and are quite robust after dyeing even without the use of mordants, resulting in significant reduction in the environmental impact. Further, inkjet printing of such biopigments has the major additional advantage of significantly reduced water & energy use .
​
These projects are funded by the Walmart Foundation in collaboration with Dr. Chih-hung Chang, Seri Robinson, and Hsiou-Lien Chen at Oregon State University


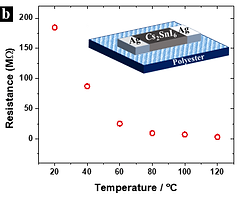
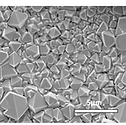


Scalable Fabrication of Smart Fabrics & Sustainably Dyed Fabrics
Dieless Room-temperature Incremental Forming of Thermoplastics
​
Thermoplastic polymer surfaces are widely used in automobiles and airplanes, packaging and biomedical implants. We have developed expertise in a dieless deformation-based process called Incremental Forming which uses simple shape-agnostic tools moving along pre-defined toolpaths to create local deformations that add up to yield a global deformation. Compared to conventional processes (e.g., molding, thermoforming) polymer IF can lower thermal costs, reduce tooling costs and expand process flexibility for prototyping and low volume production in the above applications. We have shown:
​
-
Dieless room temperature deformation of multiple thermoplastics to unexpectedly high strains.
-
Double sided incremental forming of polymers for even higher formability & geometric accuracy .
-
Effect of process parameters on mechanical properties and microstructure of the formed material.
-
Incremental forming of metal-polymer composites.
​
This project was funded by the Walmart Manufacturing Foundation in collaboration with Dr. Sundar Atre.
